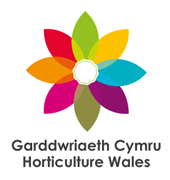
Grading is the process of sorting produce into different categories, for example size, shape, colour, freedom from pest and disease damage. Its purpose is to ensure that produce that goes on to market meets defined regulatory and retailer criteria.
Understanding market specifications
The first step in grading is to understand the specifications you are required to meet. Basic standards are written into EU law. These will apply to UK businesses throughout the Brexit ‘Transition Period’, expected to end 31 December 2020, and the expectation is that similar standards will be written into law subsequently. Many retailers have their own standards over and above these baseline requirements.
Legal standards
These are found in EU Regulation 543/2011 which sets out two types of quality standard.
- General Marketing Standards (GMS) require that all produce must be:
· Intact
· Sound (not rotten or severely bruised/ damaged · Free of abnormal external moisture · Sufficiently, but not over ripe/ developed. |
· Fresh in appearance
· Practically free from pests · Clean · Free of foreign smell or taste |
- Specific marketing standards (SMS) apply to 10 individual crops, but only apples, pears, strawberries, sweet peppers and tomatoes are likely to be relevant to Welsh growers. They are usually required product to be graded into two classes according to quality:
- Class I: Good quality produce, allowing for minor defects such as areas of slight skin defects or slight shape defects.
- Class II: Reasonably good quality produce, which may show one or more defects (depending on the product)
There is a third ‘Extra’ class for superior quality produce, that is uniformly regular in shape and appearance, only allowing some very slight superficial defects. This is less commonly used. Exactly what constitutes ‘minor defects’ or ‘reasonable damage’ varies from crop to crop and these are set the in individual crop guides, links to which can be found in the resources section.
Other regulatory standards are in place for specific crops, for example seed potatoes where the Seed Potato Certification Scheme requires product to meet strict minimum levels of key diseases to prevent the spread into ware crops. These include potato cyst nematode, blackleg and virus in the growing crop and rots, gangrene, scab and scurf in the tubers
Retailer standards
The above are minimum legal standards, but many retailers have their own additional requirements to meet the expectations of their own specific customer bases. These are usually set out in the agreements/ contracts with producers, it essential that both parties are very clear about expectations. Lack of communication can cause significant losses to growers and comprise working relationships along the supply chain.
Growers marketing directly, for example through farmers markets, box schemes and community supported agriculture projects, have the opportunity to enter direct dialogue with their customers about what constitutes a quality product. For example, many of these customers will be happy to accept odd shapes/ different sized product as long as it is fresh, nutritious and tasty.
Grading approaches
Hand/ field grading
- Where crops are harvested by hand most of the grading is usually carried out in the same operation. This represents a large saving in time and therefore money. In larger scale operations, this has led to the development of some large and sophisticated mobile rigs, as shown below for celery and daikon (mooli).
Mobile packhouse for celery (credit David Frost) |
Field grading daikon (Credit David Frost) |
For most smaller scale producers, however picking is done by hand
- In crops/ systems involving several harvesting passes, crops that are under or oversized, or under ripe remain on the plant until the next harvesting pass. Crops that do not make the quality grade can be left on the field
- Reduced handling is important for all crops and harvesting and grading in one operation helps to achieve that. This is especially important for those most prone to damage such as fruits, leafy vegetables and immature fruit vegetables (for example cucumbers) which generally have very tender skins that are easily damaged. Where possible produce should be harvested straight into the containers which they will be transported/ sold (often plastic crates or cardboard boxes)
- Access to skilled labour is essential for successful grading in the field. Workers need to achieve a particular work rate in order to harvest the crop economically. This implies they need to move the crop at a reasonably brisk pace, constantly taking spilt second decisions about what to take and what to leave, while exercising care not to damage produce. This requires a high degree of skill and experience
Machine grading
Where crops are harvested by machine, usually root crops such as potatoes and carrots, the harvested crop is transported back to the shed and passed over a mechanical grader.
Anatomy of a grader
Tubers/ roots are tipped into a hopper. The size and sophistication depends on the scale of the operation. This one will hold a trailer for (about 6 tonnes), and has belt which can control the rate at which the tubers are fed in. Smaller operations might have a 1 t gravity fed tuber. | |
An elevator then lifts them up and feeds them on to series of sizing nets, which are metal nets of variable size. The nets are bounce up and down which knocks of excess soil and filters out tubers below the net size. | |
The tubers/ roots then pass on to an inspection table where grading staff remove any that do not meet the marketing specifications. | |
Finally, they pass into the bagging unit, which is usually set up to automatically switch bags at the desired weight | |
Before grading
- When harvesting mechanically, it may be necessary to slow down occasionally to give workers time to remove as much soil and as many rots and stones as possible. This means cost, but it pays off by making grading more efficient and reducing damage caused by stones to the produce as it passes over the grader
- Minimize the drop between the harvester chute and trailer/ box/ bin to prevent bruising. Fall braking systems and box filling chutes are commonly used to achieve this. Further information is available in this guide
- Ideally it should be possible to transfer the produce from the trailer/ bins/ boxes you are harvesting into directly into the hopper of the grader. If an intermediate step is required this significantly increased the risk of damage and losses
Setting up the grader
It is important to carry out a test run before starting to grade; it invariably saves time in the long run and reduces down time for the grading staff.
- Make sure the machine is level. If it is not, product will tend to flow towards on side of the machine, increasing contact with the frame and therefore the risk of damage. Uneven distribution also makes it difficult for grading staff on the on the inspections table.
- Make sure all the belts are running smoothly and flush to the machine. If the belts are even slightly out of line, over time they move horizontally (from left to right) and eventually jam against the frame.
- Identify any gaps through which smaller tubers/ roots might fall through/ get crushed and make appropriate adjustments
- Ensure all your weighing equipment is calibrated correctly
Minimising grader damage and losses
As discussed above there are several steps involved in grading and each one carries a risk of causing damage. There are number of measures that can be taken to help reduce that damage
- When loading the hopper, minimise the ‘drop’ from the trailer/ bin/ box on to the hopper floor. Most hoppers are lined with rubber to reduce impact/ damage
- Maintain an even flow of crop to on the elevator to ensure it is separated from debris as much as possible ensuring removal of soil and potentially damaging stones
- Identify and remove any sharp edges that might cause damage. This includes edges of all conveyors, inspection tables, and bagging units. Ensure the nets are in good condition without any protrusions that could cause damage to the product and indeed other parts of the machine
- Minimise all the drops from one part of the machine to the next
- If the graded product is going into boxes rather than bags, cushion the fall with straw-filled bags or similar.
This guide provides detailed guidance
Packing
Packing is often integrated with grading. There are many aspects that need to be taken into account when considering your packing system including:
- Food safety and hygiene
- Shelf life
- Packing materials including sustainability issues
- Statutory requirements for label
This guide contains detailed information for small enterprises
Case Study: Penbryn Organic Farm, Tregaron
Tony Little and Dafydd Owen have been growing potatoes for seed and ware on this upland sheep farm for 6 years. Potatoes are grown as part of a rotation that includes pea/cereal combi-crops and forage brassicas for the sheep The area of potatoes grown varies according the point of the rotation and therefore the field size but usually 1-2 ha. They have developed a harvesting and grading system appropriate this scale of production. In addition to growing their own, they graded and packed seed potatoes grown by a network of other growers for Sarpo Potatoes Ltd.
‘We originally set the grading system for seed potatoes’, said Tony, ‘and Sarpo Potatoes Ltd, supported by a (RDP) Corporation and Supply Chain Development grant provided the grader. Our biggest challenge was finder a hopper that was compatible with the grader and did not take up too much space, which was at a real premium.’ In end they adapted the system so they could use 1t tote bags instead of the hopper, which saved considerable investment and made the best use of the room available’
Potatoes are harvested into a big bag filler. The elevator of the harvester is kept as low to reduce the drop and the bag filler is lined with rubber to reduce bruising as much as possible. They were then transferred into tote into the field and transported back to the yard.
The bag is suspended over the mouth of the elevator with a materials handler, so that the tubers trickle out of the bag and are carried up the elevator. ‘It wouldn’t be suitable for a larger operation, because the flow of and the size of the grader limits the through put. With clean, dry potatoes no breakdown you are looking at about 2.5t/ hr. However, if there are a lot clods and stones, or worse if the potatoes have to come in wet because of less than ideal harvesting conditions, that slows everything right down and puts a lot of stress on the machinery (which then breaks down frequently). Our experience has been that the ease of grading is determined by harvesting conditions – in particular the moisture contact and the presence/ absence of heavy clods.
Setting the grader up correctly is essential and taking the time at the outset to get it exactly right pays off tenfold. It is essential to make sure that all sharp edges are removed or cushioned; losses caused by grader damage can be up to 15%. Potatoes need to be handled with care at all times. ‘Treat potatoes like eggs is an industry cliché,’ said Tony ‘but it’s absolutely true!’
Harvesting into big bag filler | Grader set up |
Feeding the grader |
Resources
Marketing standards for fresh fruit and vegetables Rural Payments Agency
https://www.gov.uk/guidance/comply-with-marketing-standards-for-fresh-fruit-and-vegetables
Minimising damage AHDB Potatoes
https://potatoes.ahdb.org.uk/publications/minimising-damage-guide
Packaging for Horticulture: A practical guide for small enterprises Horticulture Wales https://horticulturewales.co.uk/wp-content/uploads/2018/11/Packaging-for-Horticulture.pdf